Background
On one hand, service, quality, ecology, fast delivery times and individual solutions cause increasing demands on packaging printing. On the other hand, there is a high degree of competitive pressure in the industry. Tight time windows, high quality standards, legal regulations and complex print jobs are forcing many market participants to constantly optimize their products and processes. Flex-Punkt and XSYS address these challenges and continuously adapt their service and portfolio to meet growing customer needs, while keeping an eye on each other’s needs as well.
Implementation
Various packaging applications need an all-rounder when it comes to flexographic printing forms. In this context, ITR (in-the-round) photopolymer sleeves are becoming increasingly important. The principle: ITR sleeves form an endless printing plate. They are imaged as a round shape, which creates no seam between the beginning and the end of the print. This allows a constant, continuous print image. Flex-Punkt finds the best result when using nyloflex® ITR products of XSYS.
nyloflex® ITR Classic and nyloflex® ITR Thin are endless ready-to-image photopolymer sleeves with a LAMS (Laser Ablative Mask System) layer for digital imaging (CtP technology). This type of printing form eliminates the need for separate plate-mounting, as well as compressible adhesive tape. Set-up times, labor and costs are significantly reduced. In direct comparison to other commercially available products, nyloflex® ITR Sleeves are characterized by an extremely high register accuracy and a longer service life, while at the same time offering better consistency in printing operation. Due to its very good ink transfer, low thickness tolerance and dot gain, nyloflex® ITR Sleeves are particularly suitable for endless print motifs in line, full-area and halftone printing.
“nyloflex® ITR Classic and nyloflex® ITR Thin are endless ready-to image photopolymer sleeves with a LAMS layer for digita,” said Patrick Lüdecke, General Manager Sleeves Global at XSYS.
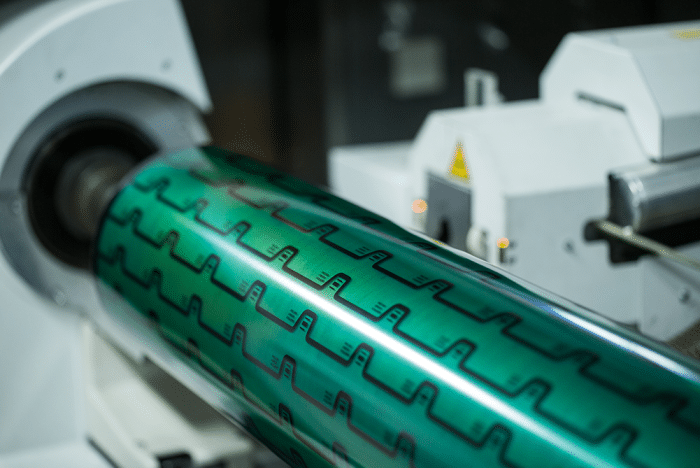
Result
Together with test customers, XSYS was able to generate an up to 20% higher print speed with ITR sleeves. Compared to plate mounting, manual intervention is no longer necessary. With nyloflex® ITR Sleeves assembly defects are a thing of the past. The digital imaging eliminates slipped printed images. Due to the accuracy of fit, the overfilling of the colors is significantly lower and a lower contact pressure is required. This allows a gentler pressure and guarantees an improved product life.
nyloflex® ITR Sleeves can be easily mounted onto a rotec® H / C adapter. This compressible adapter is available as standard with three different airflow systems (Bridge, Unifit, Airo) and is suitable for conventional cylinder and cantilever presses. Further, issues with the typical plate mounting set-up, such as air pockets and assembly defects, can now be ruled out and further shorten set-up times.
Flex-Punkt and XSYS are constantly working on possible improvement measures. One example was optimizing the special packaging needed for the sensitive surface of the pre-processed ITR sleeves. As a rule, nyloflex® ITR Sleeves are packed individually in disposable boxes. For this reason, a new environmentally friendly, reusable packaging has been tested, which allows, in some cases, accommodation of multiple sleeves. This solution has resulted in significantly improved sustainability, which is very important to both companies.
Find out more about nyloflex® ITR Sleeves.